Fabrication d’une boite à Défis écoresponsables au FabLab de la Casemate de Grenoble
Publié par ArcheInnovateurs LindGreen, le 5 décembre 2022 1.5k
Dans le cadre du parcours de l’association de l’Arche aux innovateurs (https://www.arche-aux-innovateurs.fr/) nous avons réalisé, en deux après midi, un prototype de boite à défi écoresponsables au FabLab de la Casemate de Grenoble . L'équipe du FabLab nous a formé sur l'imprimante 3D et la découpe laser avant de pratiquer, ce qui nous a permis de mieux appréhender les possibilités fonctionnelles et esthétiques de notre projet.
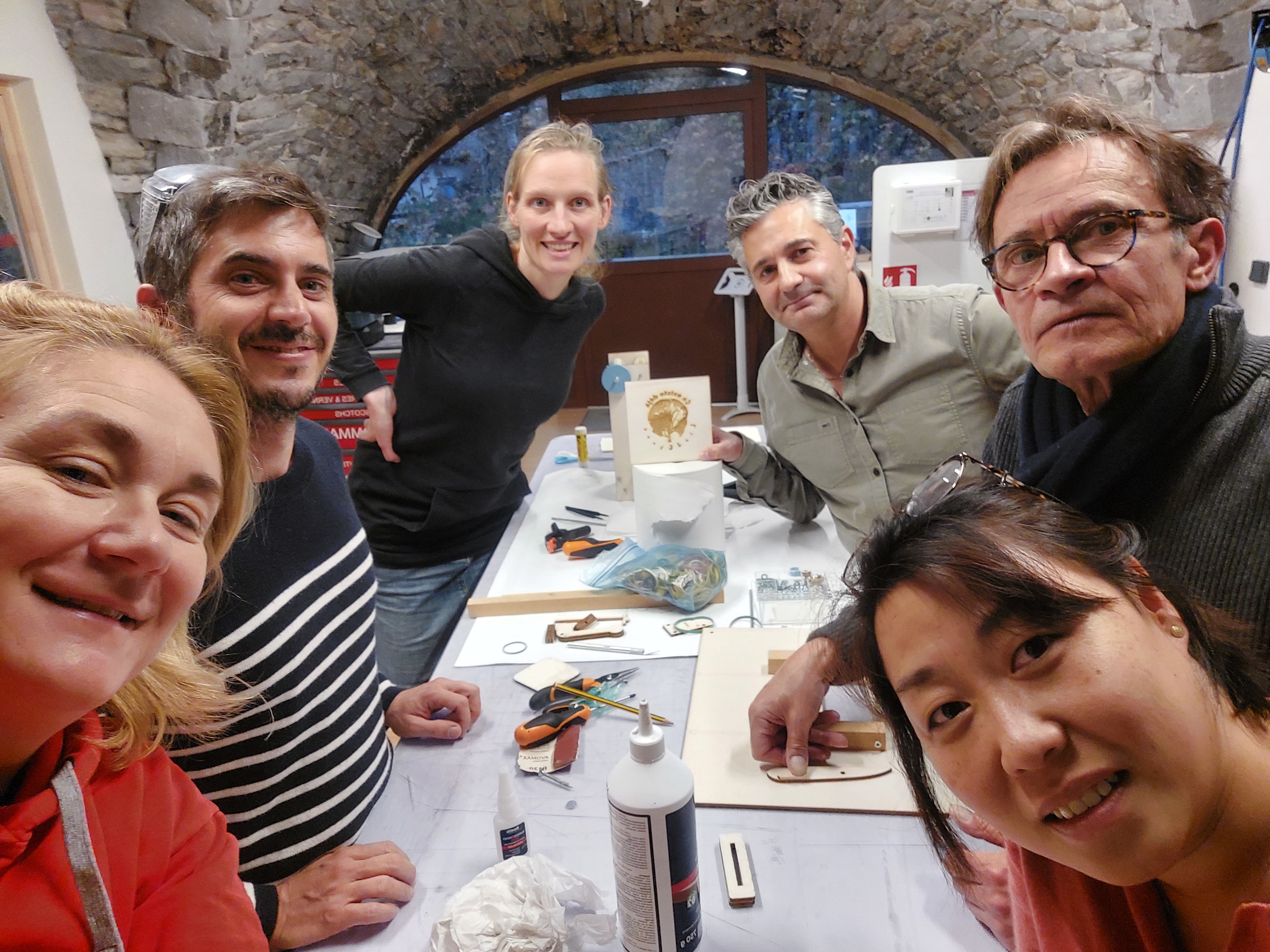
Notre équipe :
Nous sommes une équipe, baptisée LindGreen, constituée de 6 personnes, réunies au sein du parcours éco-innovation proposé par l’Arche aux innovateurs. D’horizons variés (contrôleuse de gestion, informaticien, ingénieur, marketing, scientifique, directeur commercial, enseignante) nous apprenons tout le processus d’innovation au sein d’une formation de 3 mois.
Notre projet :
Notre projet s’appelle ‘Ça existe déjà’ et l’objectif est de réaliser notre prototype final au FabLab de la casemate de Grenoble. Notre produit est un objet artistique qui propose des défis écoresponsables qui ont tous la particularité d’informer en faisant faire des économies aux utilisateurs.
Il est composé de trois parties fonctionnelles :
- Un compartiment pour recevoir des carte ‘comportement’ avec des récits personnels et anonymes de l’utilisateur sur ses actions écoresponsables. Les dépôts de cartes sont comptés mécaniquement.
- Une machine de déroulement mécanique qui présente, une par une, 20 cartes ’défi’.
- Un distributeur de cartes vierges pour noter son choix de défi si on le souhaite.
- Une partie artistique modulable au-dessus du mécanisme fonctionnel.
Nous avons fabriqué au FabLab de la casemate de Grenoble toute la partie fonctionnelle : Un dérouleur, un distributeur de cartes ainsi qu’un mécanisme permettant d’accueillir les cartes comportement, et le boîtier en lui-même.
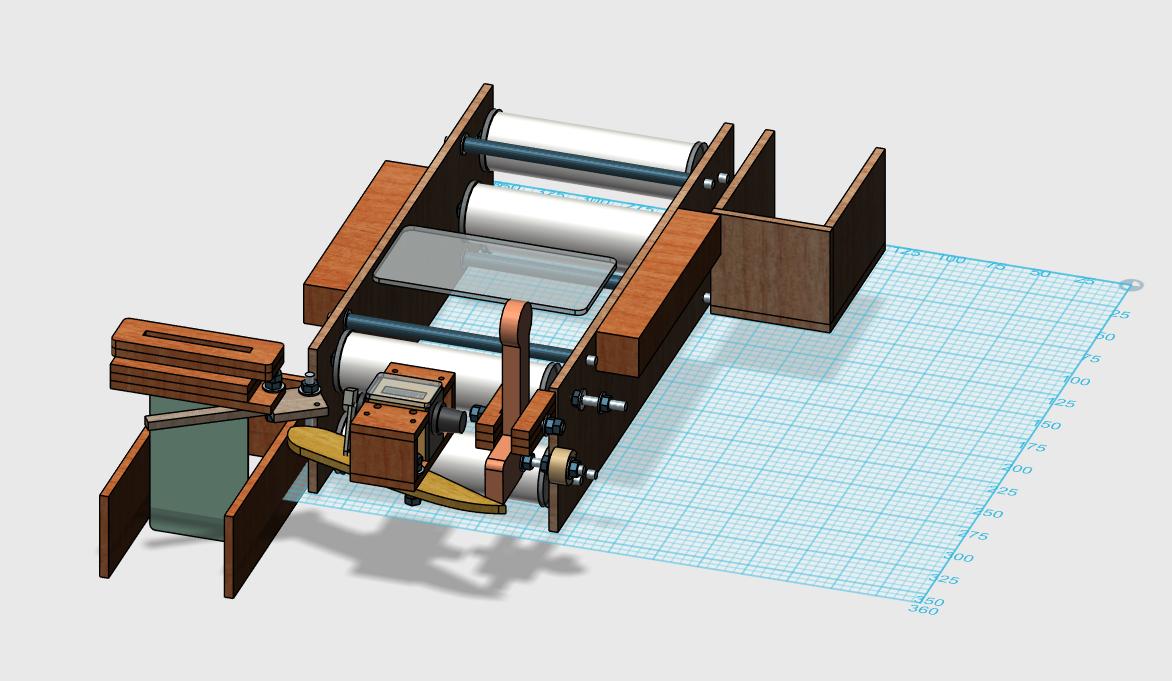
Passons maintenant au vif du sujet : la partie technique et le montage de notre produit
Étape de montage :
Nous avons commencé par nous répartir les tâches :
- Découper la bande et coller les défis en vue de la fabrication du dérouleur.
- Découpe laser du calepinage des partie en bois et en PMMA (plexiglass).
- Découpe et ponçage des tubes PVC, tiges filetées, entretoises et tasseaux de maintien.
- Collage des différents éléments constituant le boîtier et les mécanismes.
- Montage des différents éléments ensemble.
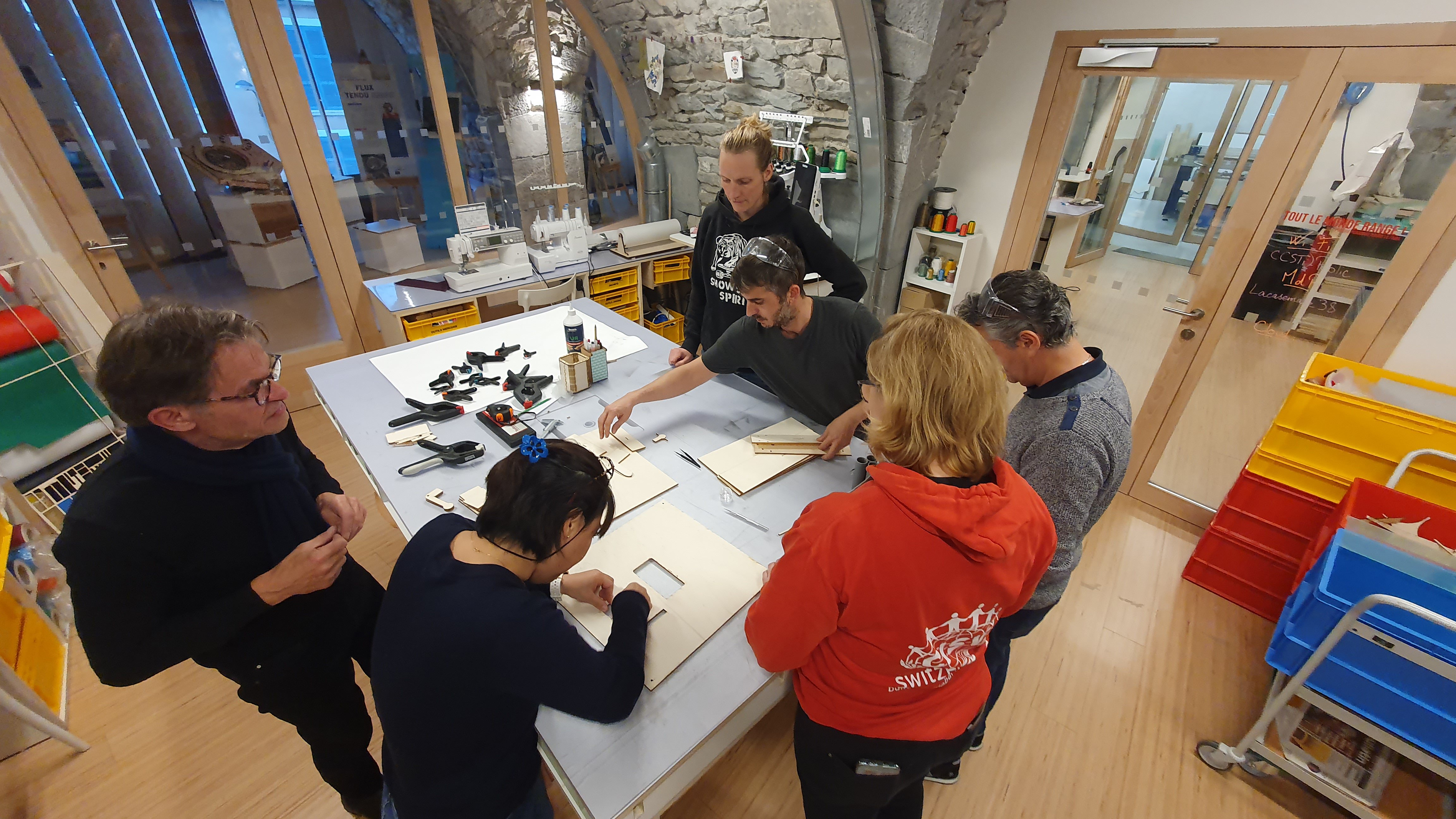
Méthode et outils utilisées :
- Découpe laser (pour le bois et le PMMA).
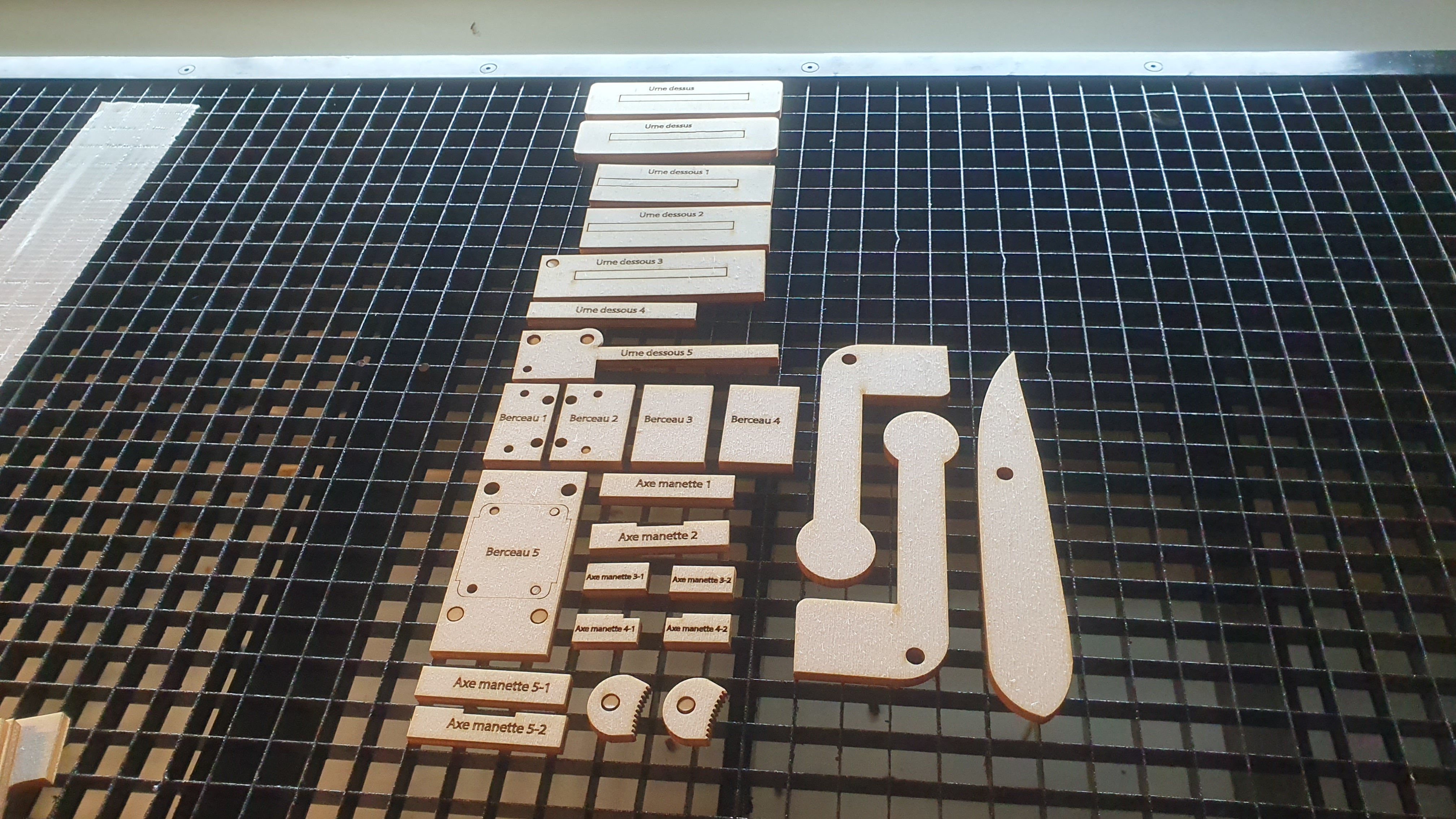
- Imprimante 3D (Pour la fabrication d’une molette).
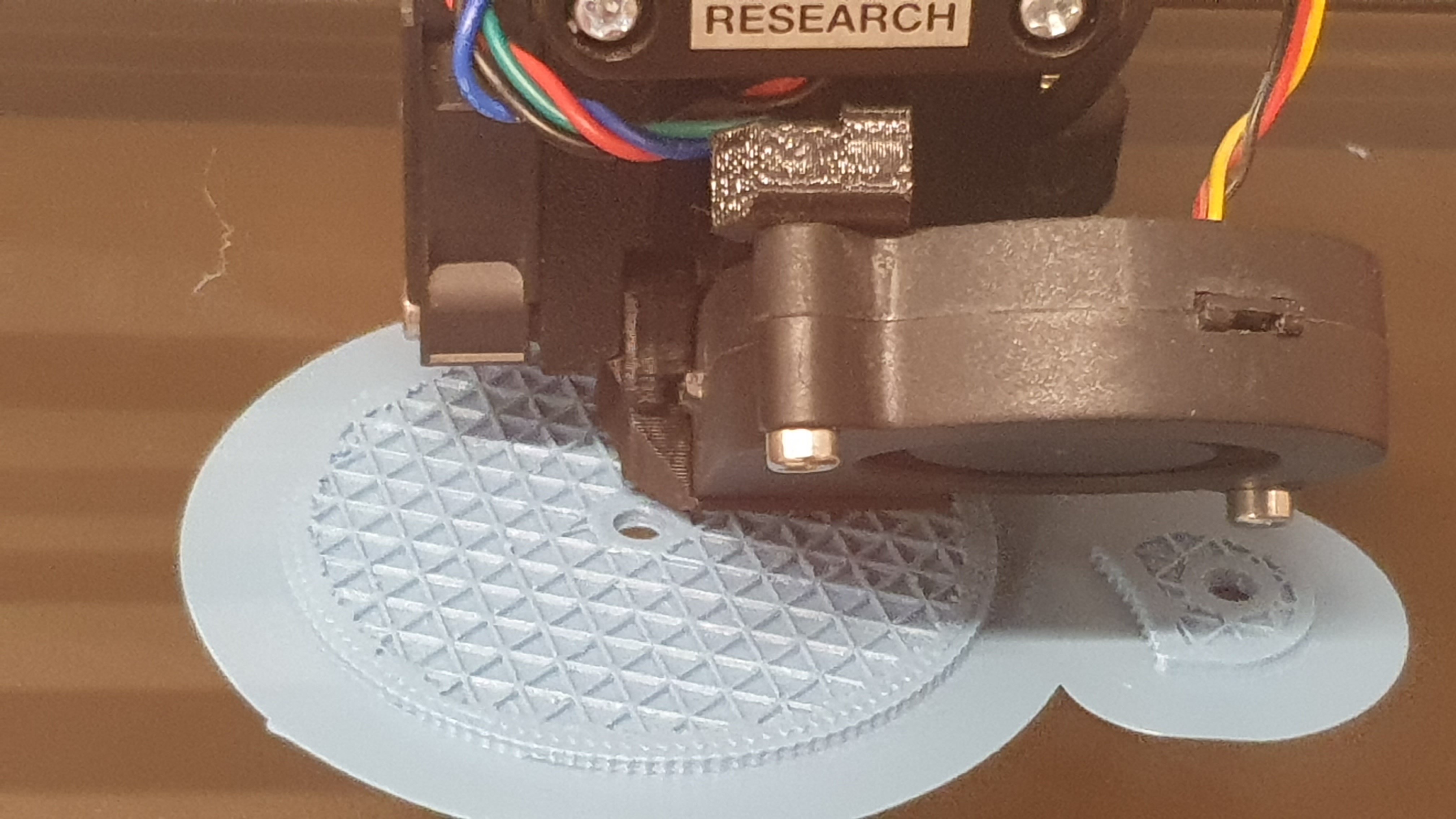
- Scie à métaux et à bois pour la découpe des tubes PVC, tiges filetées, entretoises, et des différents tasseaux de maintien.
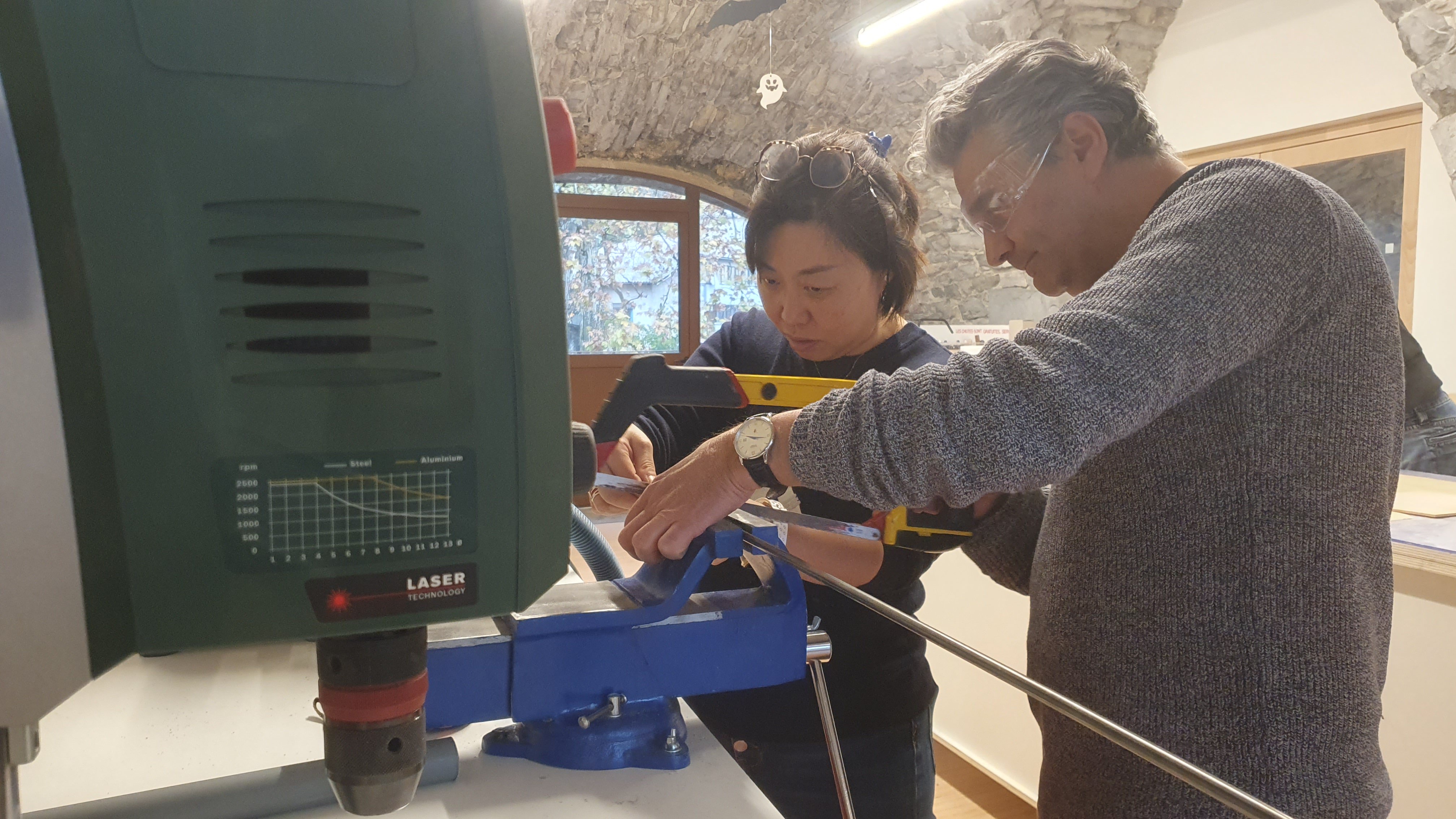
- Ponçage manuelle ou à l’aide d’une machine.
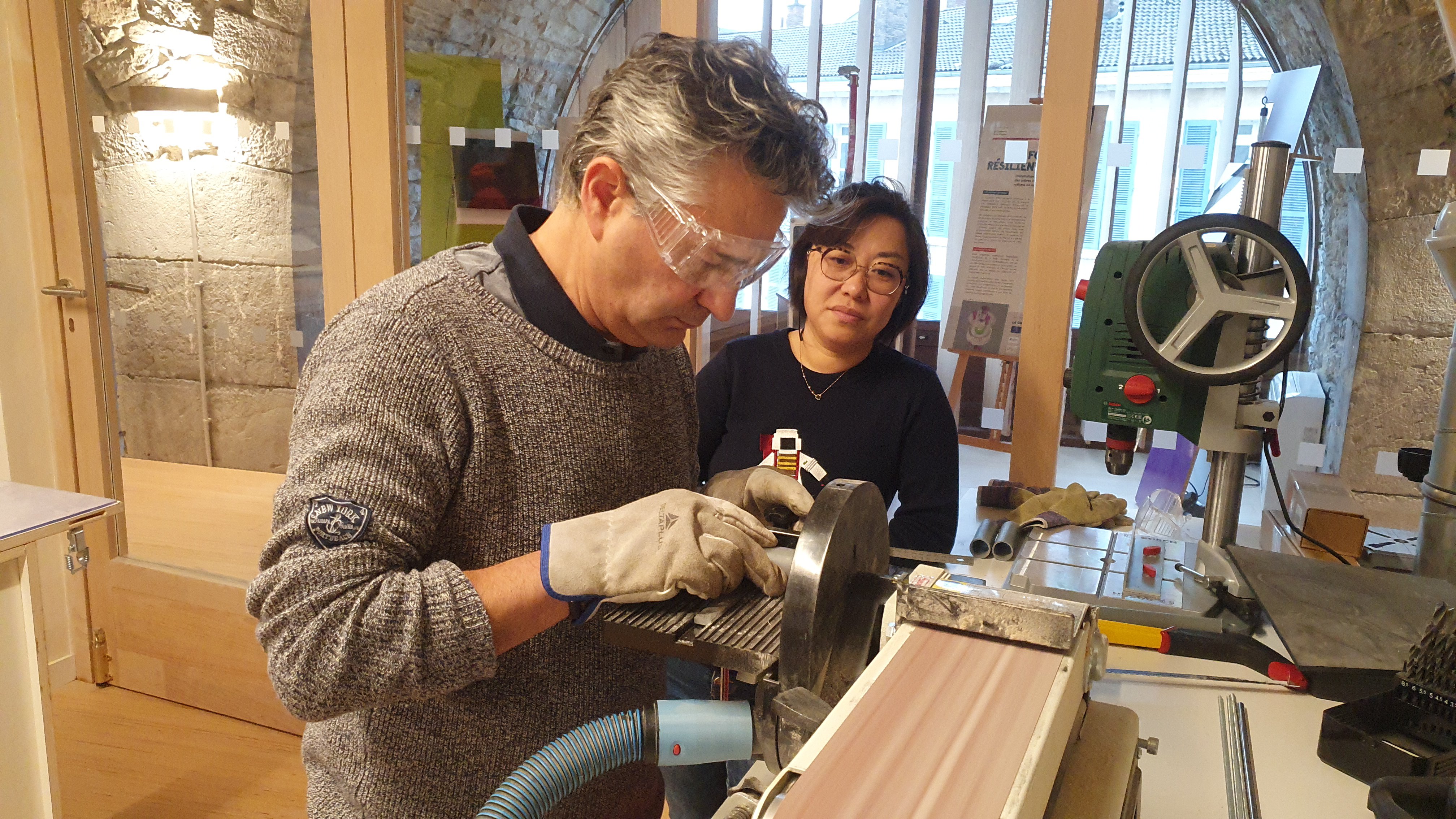
- Collage (colle à bois, Superglue).
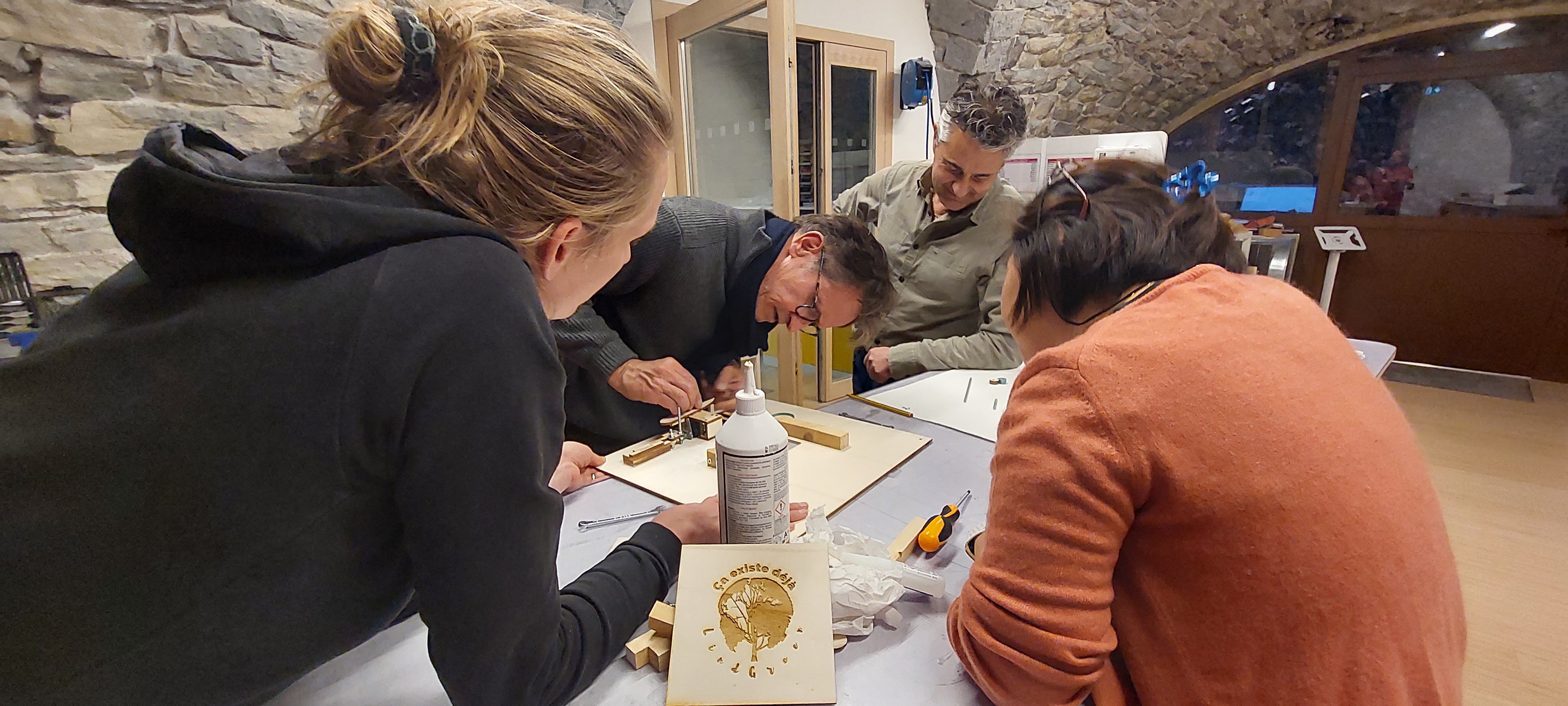
Matériaux utilisés :
- Du bois de peuplier en 5mm et du PMMA en 3mm pour la découpeuse laser,
- Du fil PLA pour l’imprimante 3D,
- Des tubes PVC,
- Des tiges filetées de 5mm,
- Des tubes de 8mm utilisés comme entretoise,
- Des vis et rondelles correspondants au diamètre de la tige,
- De la colle à bois, de la Superglue, des élastiques.
Plans de montages :
Les plans de montages ont été pensé puis modélisé sous Autodesk 123D.
Tous les tracés permettant de réaliser notre produit fini nécessitant une découpe laser ont été exportés en .svg (face par face) puis importés dans Adobe Illustrator (calepinage).
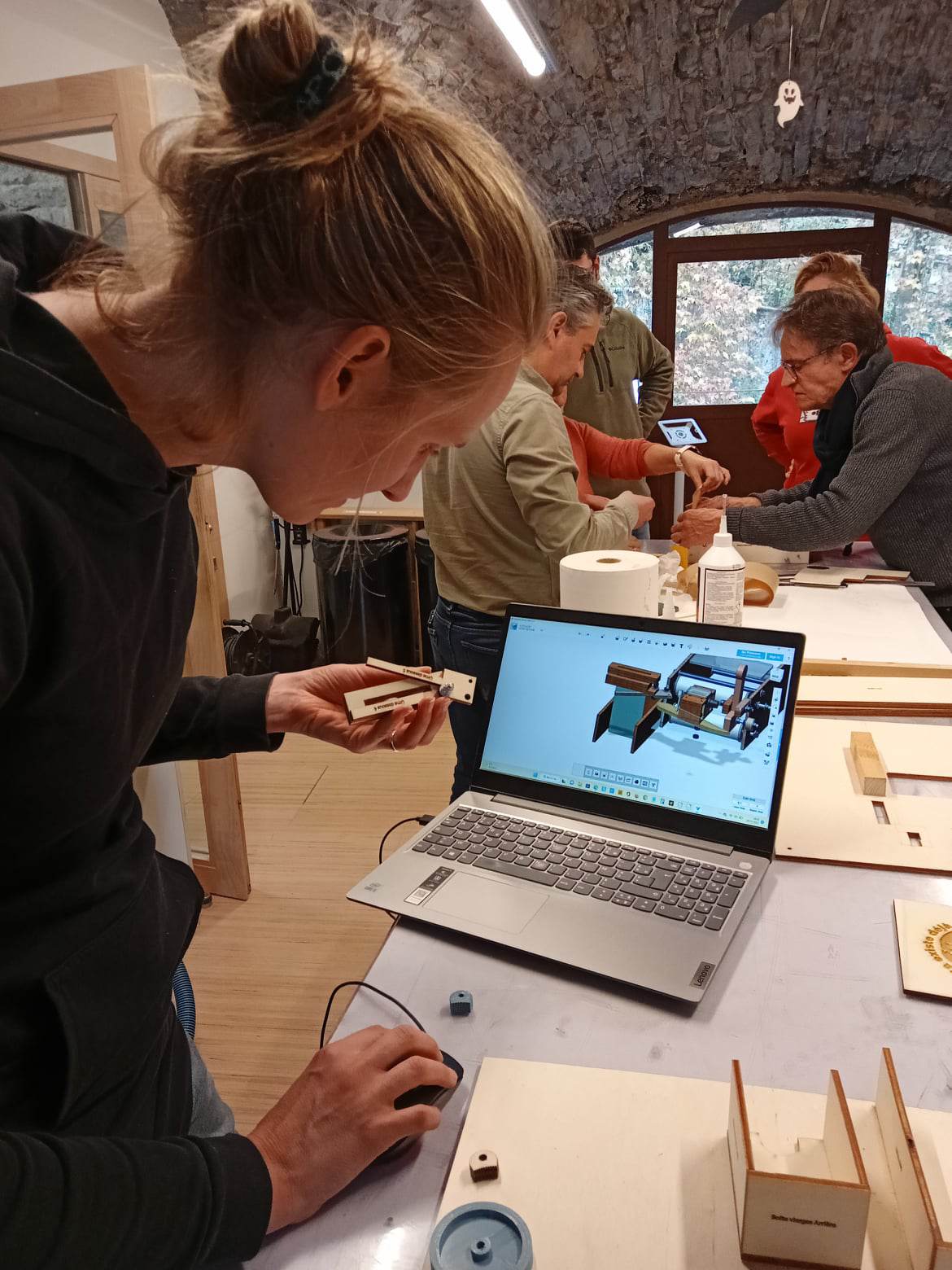
Compte-rendu :
On a déjà appris une chose primordiale, l’activité manuelle fait beaucoup pour la cohésion d’une équipe, et que Michel, notre responsable de conception au sein de la formation, ainsi que Gaétan, Fab Facilitateur / Concepteur à la casemate, ont été au petit soin avec nous. Nous n’avons pas rencontré énormément de difficultés pour la découpe des différents éléments (manuelle ou laser) ou pour ce qui est de l’impression en 3D.
La partie la plus complexe a été l’assemblage qui demandait des collages et de la précision. Il nous a fallu trouver une solution pour permettre le déroulement des défis et la mises en tension de notre bande, mais un jeu d’élastique et un peu d’huile de méninges ont fait le reste.
Nous avons également du refaire notre modèle de manette mais nous y sommes arrivés. Seul bémol le crantage de notre molette réalisé en plastique avec l’imprimante 3D n’est pas assez prononcé.
Bilan de ces trois après- midi à l'atelier FabLab de la casemate :
Notre prototype de boite à défi est désormais terminé. Tout fonctionne même si nous avons du revenir au FabLab pour faire un ajustement de manette et remplacer quelques écrous classiques par des écrous autobloquants. Notre objet final est un travail collectif, incluant notre responsable de la conception qui a trouvé les solutions que l’équipe n’avait pas su réaliser. Ça fonctionne et c’est Low tech sauf la molette qui est en impression 3D. On a même pris le temps de s’amuser et de découper et graver notre logo sur une chute de bois pour parfaire le maquillage de notre boite. Un grand merci à Gaëtan qui a été super disponible et qui favorise la manipulation pour faciliter l’apprentissage.
Ces trois après-midi FabLab ont été réellement très agréables, il y règne une belle ambiance de l’accueil à l’atelier.
